Construction Takeoff Services
As anyone working in construction will know, material takeoff services are integral to project cost estimates and bid maximization. Yet newcomers to the field may be unaware of its existence! Understanding construction takeoffs services are vital to estimate costs accurately due to rising material costs. Investing in construction estimating services help you curb cost and reduce your spending spree.
What Is Construction Takeoff Services? (What Do Construction Takeoff Services Mean?)
Takeoff in construction is the process by which contractors determine how much of each material is necessary to complete a project, with accurate cost estimation requiring this approach. Also referred to as material or quantity takeoff.
Contractors in the building industry use construction takeoffs services for various purposes, including preparing estimates and placing bids, as well as calculating how much of each item to purchase.
Submitting Bids: When bidding on any work, you must know precisely how many items will be needed to establish material prices in your bid. Without knowing this information, the risk is that either under-bidding is lost due to under-estimating or over-bidding. A precise takeoff is critical in determining the outcome of any offer made – its success lies within this crucial element.
Estimating: Determining the quantity of materials necessary is the initial step in the estimation process. You may estimate or perform a takeoff to obtain more precise figures. Once this step has been taken, prices can be set for labor hours, taxes, waste percentage, and any additional expenses arising from it all.
Determining How Much Material To Buy: Regardless of whether you are making a bid or creating an estimate, knowing how much material to purchase remains critical. Underbuying can result in multiple trips back and forth to the store for additional supplies. While overbuying can eat into earnings by decreasing returns on sales.
As can be seen, construction provides many beneficial options. There’s no excuse not to complete a takeoff when operating from blueprints. Using one could save time and money when planning projects by providing more accurate resource estimation.
The Process of Material Takeoff Services
Before undertaking takeoff, a cost estimator should carefully review project plans to ensure all required supplies are included and the proposed project meets the company’s timeframe. After counting materials such as outlets and fixtures , compute material costs according to quantities and any additional expenses to generate your estimate.
Review Your Findings
To avoid wasting time on unsuitable projects or starting your takeoff before gathering all necessary materials for an estimate, a comprehensive examination of project blueprints and specifications must be conducted. Ensure you understand the scope, planned dates, deadline, and any other specifics of the task by keeping track of everything in the invitation to bid document. Examples of such specifications could include materials or brands of manufacturers a construction architect specifies. By doing this, your attention on projects will help you win and complete effectively.
Measuring the Materials you require
Your focus should only be on projects you feel confident your business can compete and win. Such as materials you require that are necessary for construction. By being selective about which projects your attention should focus on, you’ll ensure only those worthy projects receive your consideration and dedication.
Quantity Measurement with both Manual and Digital Techniques
Quantity measurement includes measuring walls or landscape areas on drawings to calculate square footage, volume, or any metrics to ascertain how much timber or concrete will be required for your project. Previously, this was by manually using a ruler and paper. With material takeoff services, this task can now be done more efficiently. With adding components and assemblies automatically into your takeoff to determine both timber requirements and nail as per your takeoff data.
Calculating Expenses And Adding Them
After taking measurements and counts, you can determine how much material will be needed for the project. However, cost-estimating software allows you to account for more complex factors besides supplies. Markups, taxes, labor, waste disposal fees, and overhead charges, which are just some of the many expenses to consider in cost estimation for construction. Accurate estimations are essential for peace of mind. An insufficient bid could reduce profits, leaving a negative return, while an overly ambitious offer could cost the job!
Material Takeoffs and Cost Estimates
As soon as you begin working in construction, you must understand the difference between an estimate and a takeoff. A takeoff refers to calculating how many materials do you require for a task. Takeoffs don’t account for any additional expenses that an estimate might include or related material costs.
On the other hand, an estimate advances the takeoff further by including additional expenses that the contractor will face over and above applying charges to items as determined by the takeoff. Many contractors utilize building cost estimation software to help streamline this process and simplify their lives.
Who Provides Estimates and Takeoffs?
Building material takeoffs are done by contractors and subcontractors, who are experts at assessing the materials necessary for a project as they’re doing it themselves. Occasionally, certain contractors might collaborate with an cost estimator who would use their takeoff proposal as guidance and allocate costs according to specified amounts; construction cost estimation is one of the primary components of this process.
Items to Include in Your Detailed Construction Takeoffs
Contractors seeking the most accurate costs and quantities must include in their takeoffs all project-related details that could impact costs and amounts. Such as all materials to construct features and manufactured fixtures to complete projects . This adds costs but is essential.
Common materials employed by contractors when building features and structures include steel, concrete, and wood. Custom fixtures available through them may include windows, pipes, lights, and wires.
How to Conduct Construction Takeoffs
Construction takeoffs can happen either manually or electronically. Contractors performing manual takeoffs often rely on accurate plans they print off for reference when doing manual takeoffs manually using scale rulers to measure them for accurate measurements required in their takeoff.
When painting a room, measure its four walls individually to determine its square footage before deducting any negative space around doors, windows, and entryways from that total figure.
Digital Takeoffs/Takeoff Software
Summing up, digital blueprints and construction takeoff software are the foundation for digital takeoffs. After uploading your plans into the takeoff program, using its tools for takeoff measurements, you may then begin measuring walls, floors, pipe lengths, or any other objects on the layout by simply using your mouse to navigate around.
Digital takeoffs are excellent because the software handles all the computations with almost zero errors! Plus, you’ll always know exactly how much materials will be necessary!
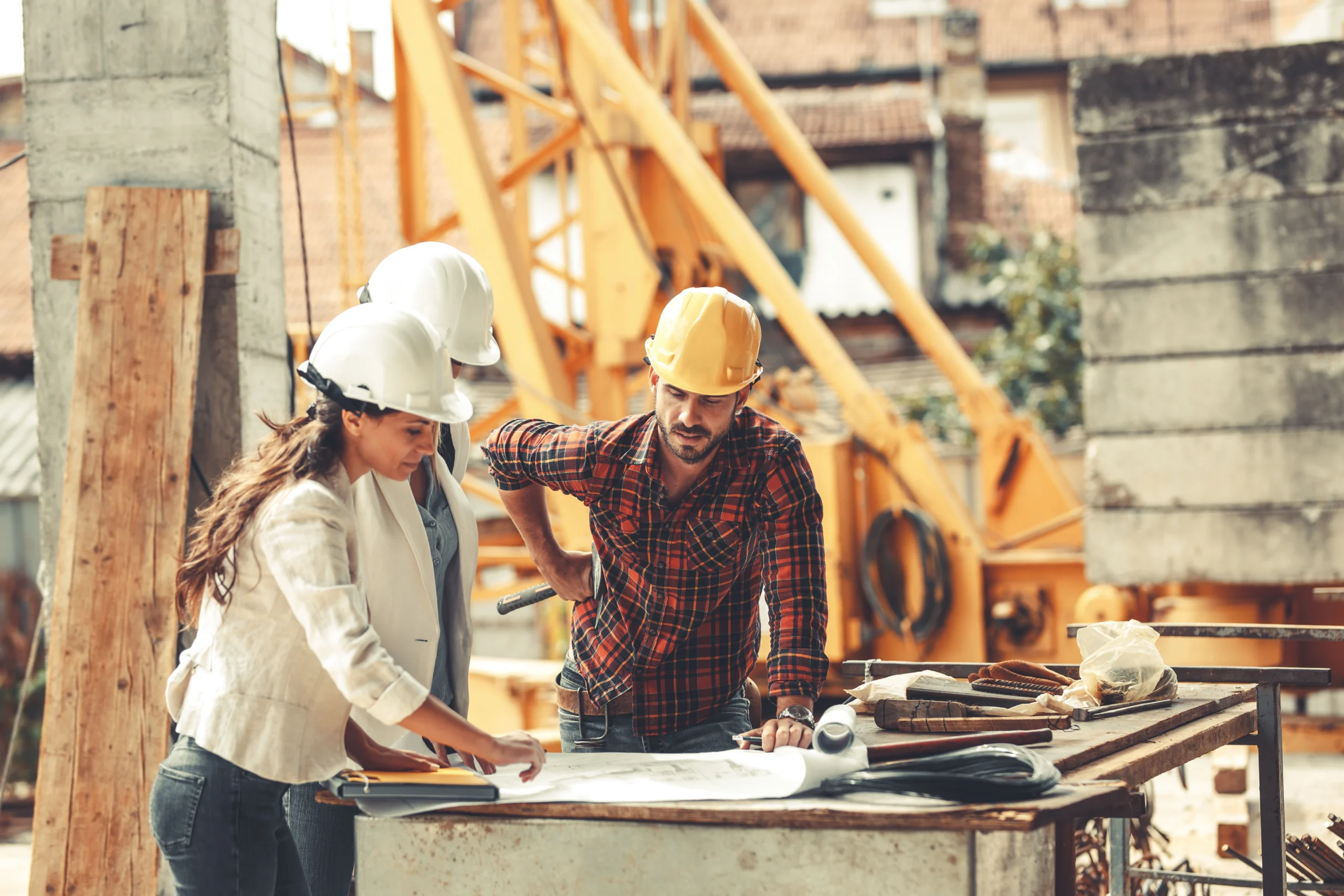
Calculating For Different Materials
Contractors may manually calculate data or use takeoff software based on the materials and resources required. Either way, contractors must provide separate information for every resource, so a cost estimator can accurately calculate costs:
Contractors must consider raw materials' dimensions when calculating to ensure accuracy, including weight and height, breadth and depth measurements.
To provide accurate pricing, contractors must include their projected requirements in their takeoff for manufactured fixtures with fixed costs.
When creating flat surfaces in their projects, contractors often turn to manufactured features like roofing and tiling materials to achieve this result. Because these elements are flat, estimators do not require measurements; to accurately price this building element, contractors must specify its coverage area to obtain accurate pricing. Contractors can better estimate pricing and prepare takeoffs for ongoing or forthcoming construction projects by understanding what will be expected from them.
Advantages of Using Estimating Software for Takeoffs
Here are the benefits of using takeoff software:
Takeoff software can make takeoff calculations significantly faster than manual takeoffs, saving hours or days while calculating takeoffs for significant projects and smaller assignments.
Manual measuring and calculator use can leave significant room for error; mistakes made can frequently prove expensive! Takeoff software offers complete control over computations to eliminate the need to correct mistakes made in error calculations.
Your plans will always be available as long as you have internet access if using cloud-based takeoff software, which can be accessed via a web browser. Access them anytime, from anywhere: on a job site, at home, or even when traveling! It's a hugely convenient resource when studying material quantities or verifying material counts.
If you have ever worked with blueprints, you are well aware of the difficulties associated with keeping track of all those plans. Every so often, it can even be challenging to locate just one! But using digital takeoff software makes this task simple - search your project name, and the plan will pop up! No more piles of plans in the office!
Construction Takeoff Services and Sustainability
Start on the right foot in your efforts to reduce waste and advance sustainable building practices by increasing precision in your construction estimates. Accurate calculations of materials required for a building project ensure accurate takeoffs that eliminate excess by ordering only what is necessary.
Less waste is produced on-site when fewer supplies are ordered than necessary, supporting more sustainable building practices. Reducing waste also lessens the environmental effects of disposal – such as landfill usage or transportation-related emissions.
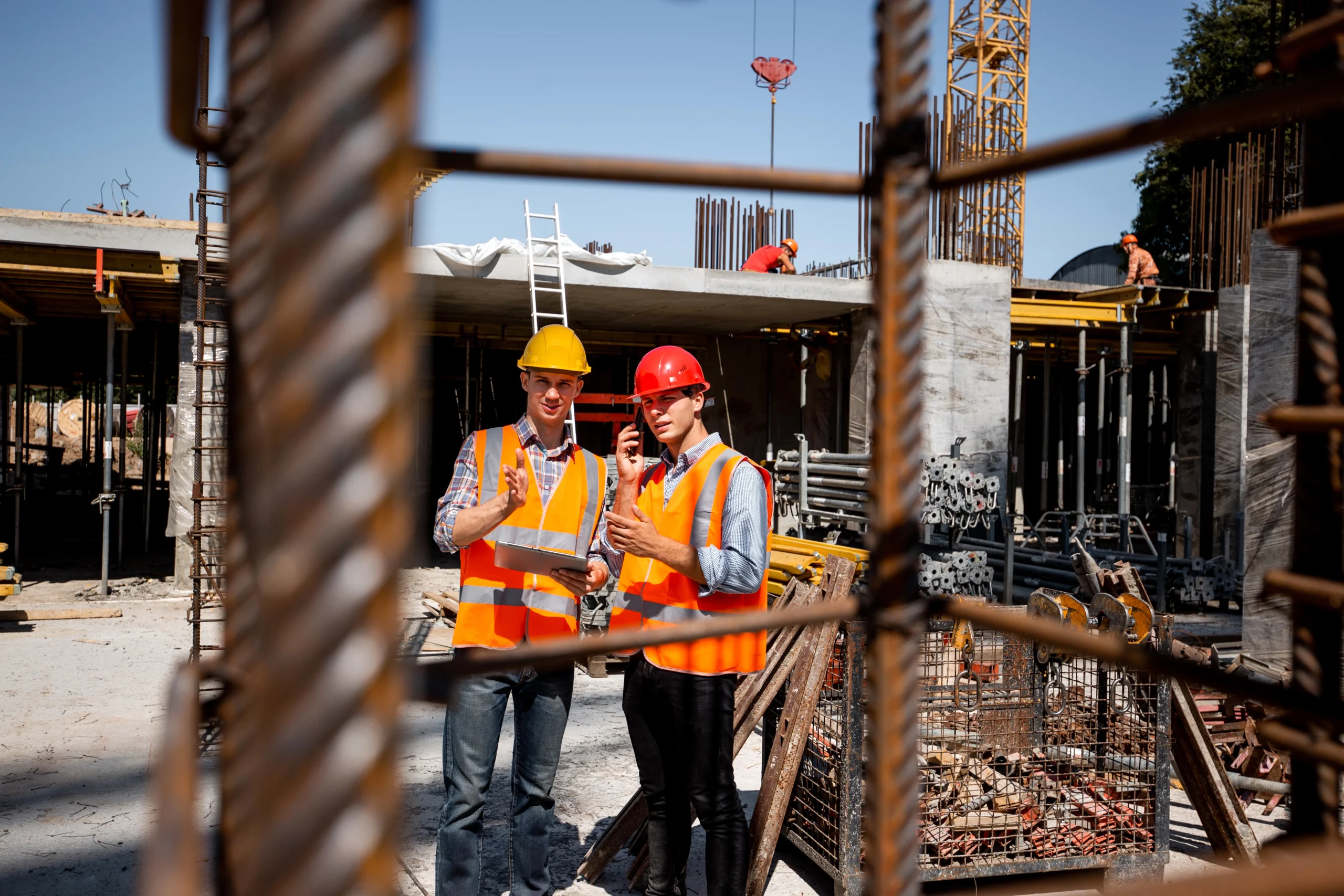
How does Our Construction Takeoff Services Fosters Results?
Accurate takeoffs facilitate effective planning and procurement methods by providing thorough information on material requirements. Maximizing resource use helps ensure materials are effective while building quality is above par. You may even save natural resources through this optimization, should it result in reduced material requirements, ultimately fostering sustainable building goals by helping select recycled, locally sourced materials with less environmental impact.
Accurate takeoffs can also play a vital role in eco-friendly construction methods. You could plan modular or prefabrication building, which often leads to less waste and greater energy efficiency, by knowing precisely the quantities of materials necessary.