To profit in the construction business, you must ensure that your expenses are paid, and profit margins are kept high. The secret is to know how much to charge for the project. Knowing the whole project expenses material, labor costs, equipment prices, and indirect costs are necessary to determine a price. Do of their bigger scale, big construction businesses frequently employ skilled construction estimators. Small builders, on the other hand, often have to do estimates themselves.
No matter how big the project is, having a precise construction estimate can be the difference between your business success or failing due to lost revenue and customers. The significance of material and construction material estimations is never understated.
An Estimate Of Materials Is What?
There are several names for a material estimate, including quantity, construction, and material takeoff. It means extracting data about the materials and quantities required for construction from the drawings. Labor, equipment, and other indirect expenses are part of construction estimates separately from the material takeoff. Thus, the only thing that is in a material takeoff is the materials.
Who Oversees When Estimating Building Materials?
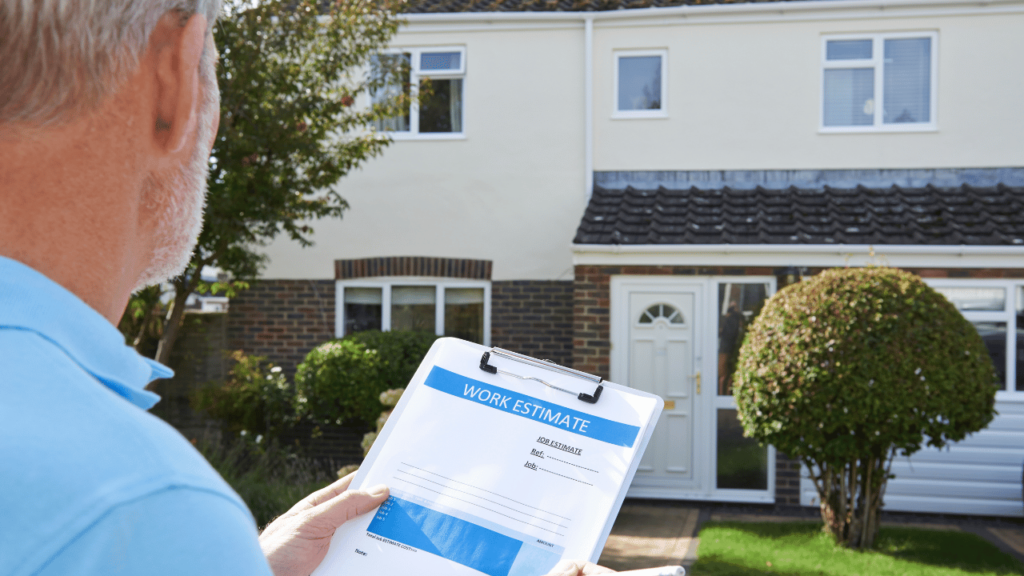
An cost estimator with specialization is the person for the job. It can be necessary for small contractors or builders to prepare the material estimates themselves. Everyone with a stake in the project, whether through the production of bids, tenders, or building budgets, ought to be aware of the project’s expenses and participate in obtaining material estimates.
When cost estimates are by hand, they are often by someone with extensive training and understanding of the construction sector.
Even a novice may do one efficiently and precisely by cost estimating software. When is the best moment to estimate the supplies needed?
Completion of construction cost estimation services must be well before the start of construction. When the task is still in its concept stage, you should provide a preliminary estimate at the very least. This might indicate whether the project is indeed possible.
A precise material cost estimate, or quantity takeoff, may be made from the drawings once you start the project. Subsequently, you may collaborate with your architect to make sure that the best building material, within the constraints of your construction project budget, is available.
Construction can start when all expenses have been determined, and a contract has been signed.
Various Ways To Calculate Material Cost Estimates
Several methods exist for counting, determining, or calculating the total number of materials when estimating building costs.
The first approach provides precise, in-depth estimations. To ensure you don’t overlook anything, we advise using a master checklist. The second estimates the surface area. On the other hand, because the third kind ignores real expenses, it is only good for an approximate estimate.
- Unit Price Method
- The Square Foot Method
- The Rule of Two Method
How To Calculate The Cost Of Building Materials For A Project
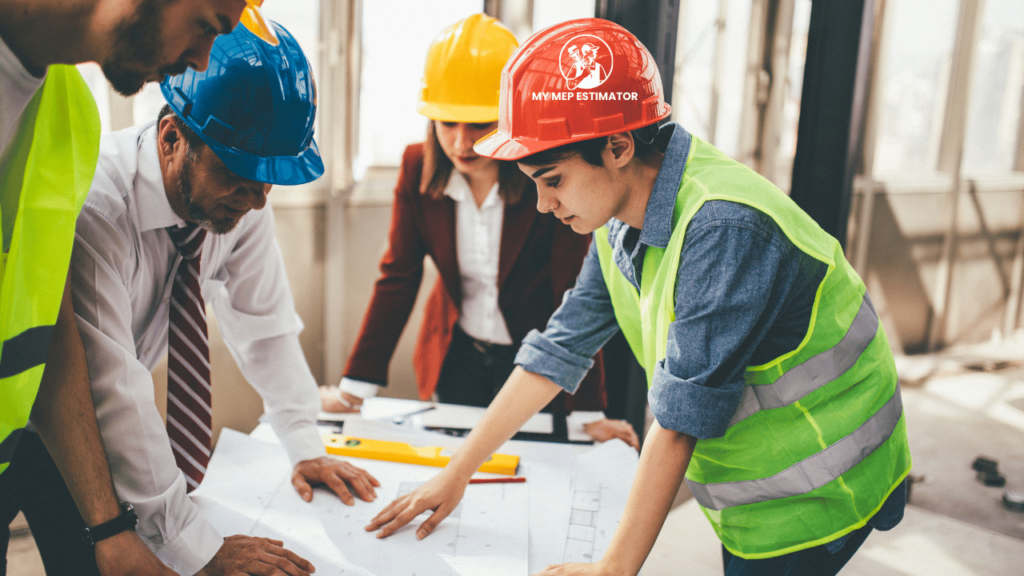
After your basic cost estimate convinces you it was feasible before you started the takeoff phase, you’ve chosen to move on with the project. The process of comprehensive estimation has now started.
The first step is picking the materials requirements to finish the job, and most construction projects will likely begin with a site visit. This will assist in identifying any problems and additional materials required to stabilize the location. The job site will generate differences even between two tasks based on the same drawing. Remember that counting all the necessary components to determine project expenses is essential.
Your Choice Matters
Selecting the goods and raw materials for your home or construction project is a step in the cost estimation. Your customer may prefer environmentally friendly materials or that a particular product might improve the site’s drainage. Perhaps the location has laws that must be followed, or perhaps some things are more or less difficult to find there. Consideration must be given to both product delivery and urgent material requirements.
You Can Get A Quick Quote From My Mep Estimator
How to Estimate Materials for Construction
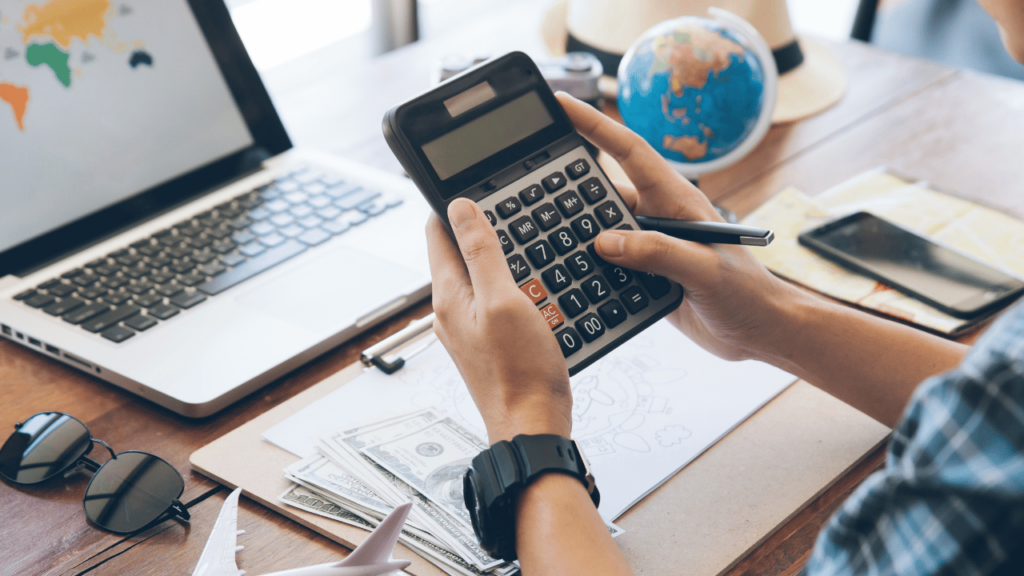
You must ascertain the material costs when you understand the square footage, quantity of material required, etc. You must do your homework or be familiar with rates if you generate your takeoff by hand.
On the other hand, cost lists and databases are readily available to you using software. Once more, if the estimate is for a project you have in the works, don’t forget to account for the effect of inflation on pricing.
A building materials estimate can be either manually or digitally. If you decide to do one by hand, you will probably come up with an approximate estimate based on your previous efforts, which should have been successful, and cross your fingers that everything turns out okay. Alternatively, you may use the more labor-intensive manual approach, count all the materials needed, and then use a calculator to get an exact cost estimate.
The computerized estimate is the alternative, 80% quicker, far more accurate, and less error-prone.
Conclusion
Having a material estimate for your construction project is a blessing. It helps keep your expenses down and lays the foundation for improvement. Not doing a material estimate can be troublesome, as you can lose money and time that will never be recovered. Estimating building materials has become mandatory for all construction projects as it ensures busy contractors get complete clarity of the costs.